*
†
FGF = fresh gas flow; NA = not applicable; VCV = volume control ventilation; Vt = tidal volume.
TABLE 24-3 PREOPERATIVE ANESTHESIA WORKSTATION CHECKLIST
Oxygen analyzer calibration: evaluates the integrity of low-pressure circuit; this is the only machine monitor that detects problems downstream from the flow control valves
Low-pressure circuit leak test: checks the integrity of the anesthesia machine from flow control valves to the common outlet; leaks in the low-pressure circuit may cause hypoxia and awareness
Circle system tests: evaluate the integrity of the system from the common gas outlet to the Y-piece
• Leak test: close the pop-off valve, occlude the Y-piece, and pressurize the circuit to 30 cm H2O using the oxygen flush valve
• Flow test: confirms the integrity of the unidirectional valves; it is performed by disconnecting the Y-piece and breathing individually through each corrugated tube
FIGURE 24-1. Draeger Medical Fabius GS anesthesia workstation (A) and GE Healthcare Aisys anesthesia workstation (B).
3. Regulators downstream from the O2 supply source adjust the pressure to about 14 psig before entering the flow meter assembly.
4. Flow control valves separate the intermediate-pressure circuit from the low-pressure circuit (the part of the machine that is downstream from the flow control valves). The operator regulates flow entering the low-pressure circuit by adjusting the flow control valves. After leaving the flow tubes, the mixture of gases travels through a common manifold and may be directed to a calibrated vaporizer.
5. A one-way check valve located between the vaporizer and common gas outlet prevents backflow into the vaporizer during positive pressure ventilation.
6. The O2 flush connection joins the mixed-gas pipeline between the one-way check valve and the machine outlet. When the O2 flush valve is activated, the pipeline O2 pressure is reflected in the common gas outlet.
B. Pipeline Supply Source. Most hospitals have a central piping system to deliver medical gases such as O2, N2O, and air to the operating room at appropriate pressures for the anesthesia workstation to function properly.
C. Cylinder Supply Source. Anesthesia workstations have E cylinders for use when a pipeline supply source is not available or if the pipeline system fails.
1. An E cylinder of O2 with a pressure of 1,000 psig and used at 5 L/min would be depleted in 1 hour.
2. A regulator for E cylinders of O2 is available that permits controlled delivery of oxygen via a nozzle at flows of <25 L/min for patient transport.
3. A full tank of N2O generates approximately 1,600 L of gas, and as long as some liquid is present in the tank, the pressure remains 750 psig. (Gas available cannot be determined from the tank pressure gauge.)
D. Flowmeter assemblies precisely measure gas flow to the common gas outlet. Depending on the setting of the flow control valve, gases flow through variable orifice, tapered tubes at a rate indicated by the position of a float indicator in relation to a calibrated scale.
1. At low flow rates, the viscosity of the gas is dominant in determining flow; density is dominant at high flow rates.
2. Safety features include the use of standardized colors for each gas, an O2 flow meter dial that is distinct from the others, and positioning of the O2 flow meter immediately proximal to the common gas outlet to minimize the chance of delivery of hypoxic mixtures in the event of leaks in the flow meter assembly.
3. Problems with Flowmeters
a. Leaks are hazardous because flow meters are located downstream from all machine safety devices except the O2 analyzer. The use of electronic flow meters and the removal of conventional glass flow tubes help eliminate this potential source of leak and risk for delivery of hypoxic gas mixtures (minimized if the O2 flow meter is located downstream from all other flow meters).
b. Inaccuracy of flow measurement may occur (dirt or static electricity may cause a float to stick)
c. With an ambiguous scale, the operator reads the float position beside an adjacent but erroneous scale (this is minimized by etching the scale into the tube).
E. Proportioning systems are designed to prevent creation and delivery of a hypoxic mixture when N2O is administered.
VII. WEB-BASED ANESTHESIA SOFTWARE SIMULATION: THE VIRTUAL ANESTHESIA MACHINE (Fig. 24-2)
FIGURE 24-2. The Virtual Anesthesia Machine Simulator, an interactive model of an anesthesia machine (A) and GE Healthcare Aisys anesthesia carestation (B).
TABLE 24-4 VAPORIZER MODELS AND CHARACTERISTICS
VIII. VAPORIZERS (Table 24-4)
A. Variable-Bypass Vaporizers
1. The GE Datex-Ohmeda Tec 4, 5, and 7 and the North American Draeger Vapor 19n and 2000 series are classified as variable-bypass (method for regulating output concentration), flow-over, temperature-compensated, agent-specific (keyed filling devices), out-of-breathing circuit vaporizers.
2. Basic Operating Principles
a. As gas flow enters the vaporizer’s inlet, the setting of the concentration dial determines the ratio of flow that goes through the bypass chamber and through the vaporizing chamber. The gas diverted to the vaporizing chamber flows over the liquid anesthetic and becomes saturated with vapor.
b. The amount of gas diverted into the vaporizing chamber is primarily a function of the anesthetic vapor pressure. A temperature-compensating device helps maintain a constant vaporizer output over a wide range of temperatures.
3. Safety Features (Table 24-5)
4. Hazards (Table 24-6)
B. The GE Datex-Ohmeda Tec 6 vaporizer for desflurane is an electrically heated, pressurized device specifically designed to deliver desflurane.
TABLE 24-5 SAFETY FEATURES OF VARIABLE-BYPASS VAPORIZERS
Agent specific: keyed filling devices
Filler port placed at a maximum safe liquid level: prevents overfilling
Secured to vaporizer manifold: prevents tipping and spillage of liquid anesthetic into the bypass chamber and delivery of an overdose
Interlock system: prevents simultaneous delivery of more than one volatile anesthetic
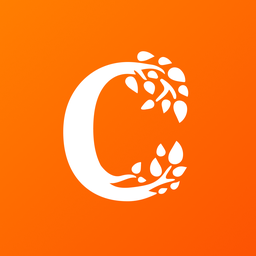
Full access? Get Clinical Tree
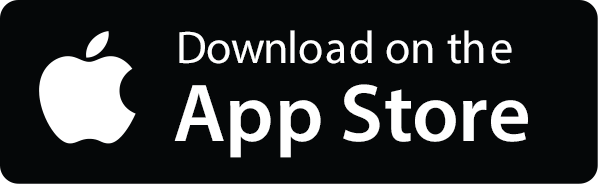
