Introduction
After the public demonstration of ether anesthesia by William Thomas Greene Morton in 1846, the need for an apparatus that will be able to deliver a fixed proportion of anesthetic vapor at an appropriate flow raised. The first anesthesia machine was built by James Taylor Gwathemy, the first president of the American Association of Anesthetists in 1912. But the machine which caught most of the public interest was the one made by Henry Edmund Gaskin Boyle in 1917, as it was publicly demonstrated at the Royal Society of London. Later on, the Boyle’s machine was patented by British Oxygen Company (BOC), and several advances from Boyle basic to Boyle E, Boyle F, Boyle G, Boyle H, Boyle M, Boyle Major, and international models were released in the market.
However, the modern anesthesia delivery systems are no longer referred to as anesthesia machines, but rather as “anesthesia workstation” (Fig. 45.1). American Society of Testing and Materials (ASTM) describes anesthesia workstation as “a system for administering anesthesia to the patients consisting of gas supply devices, ventilator, monitoring devices, and various safety features.” Although the modern anesthesia workstation is well advanced than the traditional Boyle’s machine, it retains the basic architecture and the working principle put in a technologically advanced manner. A thorough understanding of the working of the anesthesia machine and various troubleshooting maneuvers is one of the necessary skills of the anesthesiologist.
There are many different companies manufacturing anesthesia workstations like Penlon, Drager, Datex Ohmeda, Space Labs, etc., all of which have a different look. Still, the basic design of all the workstations is similar. All the modern anesthesia workstations can perform essential functions such as providing oxygen, inhalational anesthetic vapors in a precise mixture, providing mechanical ventilation, monitoring of the patients’ hemodynamic parameters as well as anesthetic gas concentrations and also effectively preventing theater pollution by foolproof scavenging systems. All these components are mounted on a box-shaped metallic structure and antistatic wheels, which gives it stability and prevents the generation of static electricity. The modern anesthesia workstation gets operated electrically, but it has a battery backup that supplies enough to work up to 60 minutes in case of power failure. While one wonders what other safety features the modern anesthesia workstation offer, it is wise to remember that each and every component of anesthesia workstation has its own significance and puts a foot forward for the safety of patients.
All the modern anesthesia workstations consist of a series of pipelines that deliver the oxygen and the various carrier gases like medical air or nitrous oxide (N2O) from a higher pressure in the hospital’s supply to a lower pressure amenable to patient’s safety. The components of the modern anesthesia workstation can be broadly classified as follows:
The schematic arrangement of the above components is shown in Fig. 45.2.
High-Pressure System
The high-pressure system starts from the cylinders attached to the anesthesia workstation and ends at the primary pressure regulator. Each machine has at least two slots for attachment of the cylinders at the back, which is called the yoke. The medical-grade cylinders are made up of an alloy of molybdenum and steel, which is stronger and thinner, making them lighter and easy to carry around. Each cylinder has a body, shoulder, and stem and is generally color-coded. The standard color coding used in India is shown in Table 45.1.
Apart from the color coding, the contents of the cylinder, chemical symbol, physical state of the contents, size code, etc., are mentioned in the label on the cylinder. The stem of the cylinder also has a valve and pressure-regulating device to prevent bursting of the contents in case of a disaster. The cylinders can have either gaseous contents like oxygen, nitrogen, air, and helium or liquids like nitrous oxide and carbon dioxide. The cylinders are labeled according to their sizes from A to J, A being the smallest and J being the largest. The size E cylinders are generally attached to anesthesia workstations. A filled E type oxygen cylinder has a pressure of 1900 psig (pounds per square inch gauge) and can deliver up to 660 L of oxygen. A full N2O cylinder has a pressure of 745 psig and can deliver up to 1590 L of N2O. As oxygen is in the gaseous state in the cylinder, the contents of the oxygen cylinder can be estimated using the pressure. Still, the N2O cylinder is generally weighed to determine its contents as it is in liquid form. Checking the cylinder pressure is one of the steps incorporated into the daily anesthesia safety check, and a pressure less than half of the full cylinder is accepted as a cut-off to change the cylinder.
Another safety feature related to the cylinder is the pin index safety system (PISS). It is a noninterchangeable safety system that prevents attachment of incorrect cylinder to the yoke. The neck of the cylinder has two small holes, which are positioned in a way that they fit into the pins in the hanger yoke of the anesthesia workstation. The position of the pins around the cylinder outlet port of the yoke is in the manner of a circle with an arc of radius 9/16th inch. They are labeled as 1 to 7 and 1 to 3 on the right-hand side, 4 to 6 on the left-hand side, and 7 in the center. The pin index of the commonly used medical gases is described in Table 45.2.
The cylinders attached to the hanger yoke of the anesthesia workstation act as a backup in case of emergency when the other pipeline supply fails. So, they should be checked regularly and kept closed after checking in order not to empty the contents after pipeline failure without knowing it. The attachment of the cylinder to the yoke is protected by a gas-tight seal, which allows only unidirectional flow of contents into the workstation but not vice versa. Once the contents of the cylinder open up into the workstation, there is a filter that prevents the delivery of grease and debris from the neck of the cylinder into the machine, and there are pressure gauges which depict the pressure of the cylinder at the front of the workstation. Next to the pressure gauge is the primary pressure regulator, which reduces the pressure of the gas to as low as 45 psig and marks the end of the high-pressure system of the workstation. This pressure is lower than that of the central pressure system, that is 55 psig, which allows preferential utilization of pipeline supply even when the cylinder is open.
Intermediate-Pressure System
The intermediate-pressure system of the anesthesia workstation consists of the pipelines which come from the manifold, oxygen pressure failure devices, oxygen flush, auxiliary oxygen flow meters, and secondary pressure regulators. The pipelines are generally the main source of supply throughout the hospital and have a pressure of 50 to 55 psig, depending on the country’s guidelines. The pipeline supply is generally accessed by a series of wall mounts attached through quick connectors. Each quick connector is again color-coded with oxygen being white, N2O being blue, and vacuum being yellow to add up to the safety features of the anesthesia workstation. These pipelines get connected to the workstation through a special set of connectors called diameter index safety system (DISS) in the United States or non-interchangeable screw thread (NIST) in the United Kingdom. These connectors prevent the attachment of the incorrect gas into the workstation.
As soon as the gas from the pipeline enters the workstation, there is a filter that prevents the entry of any particulate matter into the workstation. The pipeline pressure gauge follows the filter and displays the pipeline pressure on the front of the machine. One of the main goals of the workstation should be not to deliver a hypoxic mixture to the patient even if one attempts to do so. The ASTM standards state that any anesthesia workstation should be designed so that when the oxygen supply is reduced to the minimum allowed by the manufacturer, the oxygen concentration at the common gas outlet should not be less than 19%. So, a sensor is placed in the intermediate-pressure system, which gives an audible and visible alarm to the anesthesiologist once the pressure falls below the manufacturer-set minimum.
The other interesting feature of the intermediate pressure is the oxygen failure protection device, also popularly known as the “fail-safe.” Depending on the manufacturer, the device either proportionately decreases the flow of other gases or shut down other gases in case of an oxygen failure. But it is not as foolproof as it sounds, because it depends only on the pressure in the oxygen pipeline and can be overcome if some other gas passes through that line with the same pressure.
Oxygen Flush Valve
One more safety feature added in the intermediate-pressure system would be the oxygen flush valve, which upon activation delivers 100% oxygen at a flow rate of 35 to 70 L/min directly from the pipeline bypassing the low-pressure system and the vaporizers. Several hazards such as improper activation of the flush valve, leading to dilution of the anesthetic gases, causing awareness, and risk of barotrauma in case of a stuck valve in the open position, have been described. To prevent these, the oxygen flush valve is always not easily accessible in the modern anesthesia workstations unless someone activates it voluntarily. It also is useful in case of jet ventilation when oxygen at a higher pressure is needed, but most modern anesthesia workstations do not have the fresh gas outlets accessible. Oxygen flush and auxiliary flow meter are the parts of the workstation which works even when the machine is not electrically powered but connected to a pipeline system.
Auxiliary Oxygen Flow Meter
It is a separate flow meter mounted on the machine, which provides oxygen directly from the intermediate-pressure system, bypassing the low-pressure system. It is useful in the following:
Administering oxygen via a Hudson facemask or a venturi mask during regional anesthesia or sedation.
For apneic oxygen administration in case of a difficult airway.
One must be cautious to ensure that the source of oxygen here is the same as the pipeline, and this cannot be used in case of failure of pipeline supply, or suspicion of any crossover of pipelines wherein the backup cylinder will be helpful.
Finally, the intermediate-pressure system ends with secondary pressure regulators, which reduce the pressure to 15 to 30 psig before passing the anesthetic gases into the low-pressure system.
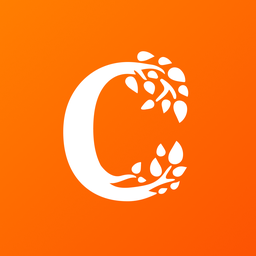
Full access? Get Clinical Tree
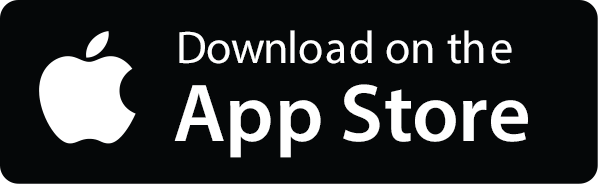
